一、设备性能参数及使用要求
2216-166.67/10.5-50 型氧气压缩机,是某制氧机厂根据我厂的工艺要求专门设计制造的,该机组为立式二列二级双缸双作用活塞式压缩机,气缸为无油润滑,活塞推力为16t ,吸入状态下排气量为l.00×l04m3/h ,吸人压力为1.05MPa,排气压力为5.OMPa ,活塞行程为240mm ,一级气缸直径370mm ,二级为255mm ,转速为428r /min,冷却水耗最为85t/h ,配用电机为850kw 、14极同步电机。全机组包括主机、冷却器、缓冲器、同步电机、润滑系统、水冷却系统及电、仪控制系统。压缩机通过刚性联轴器直接与电机相连接。
本机具有一定的自动化操作水平,吸人及排出工况的变化可通过中间气动薄膜调节阀自动调整以适应氧气量的变化。
鉴于氧气系统禁油的特心、,玉缩机运动机构部分采用无油润滑,活塞不、导向环、密封环均采用填充聚四氟乙烯制成,同时为了防止运动机构的油雾带人气缸部分,在机身上部装有刮油器,使活塞杆上的液体油被刮下来,在刮油器上部引出一接管与真空泵相连,将刮油环后的油蒸汽抽出,使机组安全可靠的运行。
二、冷却器的损坏故障
本机组采用的2 台冷却器结构完全相同,系管壳式换热器,管程通气体,为两程;壳程通水,用盘环形折流板增加水的流速,提高冷却效果,冷却管与管板的连接采用胀接方法连接。冷却水采用闭路循环,冷却水是否正常由水监视箱中的窥视镜来监视,同时当水流量低于规定流量时有声光报警。1994 年5 月,该机出口温度超标,当时没有查出超温原因,决定继续运行,直到同年8 月因二级人口超温、超压,被迫停机拆检活门,拆开后看到活门腔内有撕裂的不锈钢板,经检查活门部位,除活门片损坏,其它部件完好,进一步分析认为此不锈钢板来自冷却器,随即拆检一级气体冷却器, 看到二级气体冷却器气腔隔板已撕掉一块(见图1)。由此分析,出口超温的原因是二级气体冷却器气腔隔板损坏,气体走短路所致,拆开一级气体冷却器看到气腔隔板确已断裂。
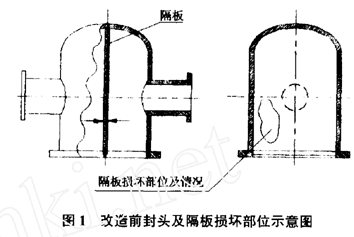
三、冷却器气腔隔板损坏原因分析
1.气流脉动和管路振动引起。在距一级气体冷却器出口管(规格:φ 159mm x6mm ,材质:ICrl8Ni9Ti )约300 ~处接一级安全阀引管(规格:φ57mm x 3mm ,材质:ICrISNigTi ) ,由于该引管较长,在1 年时间内先后4 次在两管连接处振裂。
2.冷却器支架设计不合理,产生共振引起。该机组冷却器设计为立式放置,用3 根长2m 的12#槽钢周向均布支承,在运行过程中,该支架剧烈颤动。
3.冷却器气腔隔板本身存在设计缺陷。该机冷却器气腔隔板为700mm x 530mm x12mm , ICrl8NigTi 板。在运行过程中,气体压力较高,流量较大,隔板强度不足,且在开车瞬间隔板两侧压差较大,产生共振。
四、改进措施
l 、缩短安全阀引管的长度,并将安全阀引管的φ57mm x 3mm 的ICrl8Ni9Ti管改为φ57mmx6mm 厚壁管节与冷却器出口φ159 mm x 6mm、ICr18Ni9Ti 管焊接,这样可避免安全阀引管在焊接过程中过热 或冷却器出口管焊不透而产生的焊接缺陷,从而杜绝在运行过程中连接处振裂事故的再次发生。
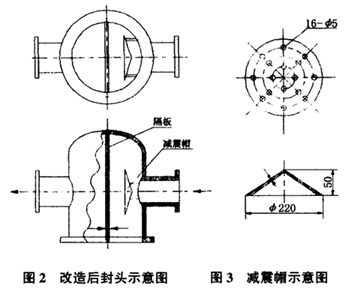
2.增强冷却器支架的刚度,在原支架上对焊同型号槽钢,支架中部、下部用槽钢连为一体,支架底部用混凝土浇注。
3.根据计算将冷却器封头由原

=12 的ICrl8NigTi 板整体刨掉,改用

=20 的ICrl8NigTi 板,同时在进气侧加装减震帽(见图2 、图3 )。鉴于该设备的使用特点,制定严格的焊接工艺及要求:
( l )将原隔板刨掉,并将焊瘤打磨平整、干净;
( 2 )按要求制作

=20 隔板;
( 3 )焊前,封头内表面及隔板表面涂抹保护层,以防飞溅物附着;
( 4 )采用双面焊接,确保连接强度;
( 5 )焊后打磨平整、探伤,清理干净并脱脂。
五、结论及建议
通过上述改进措施,解决了因设计不善在使用过程中出现的问题。改造后隔板损坏现象没再发生,从而保证了氧压机的安全运行。建议制造厂家在设计时应充分考虑到该设备的使用条件和特殊要求,从设计、制造方面给予解决,不把隐患带给用户。